Turks Heads
Direct formation of round material to squares, rectangles & special shapes
Custom Built for You ~ Designed by FENN
FENN engineers take the time to design and build the right turks head machine to fit your wire forming and shaping specifications, and fulfill your unique production requirements. With experience building standard metal forming equipment, and customized metal forming machinery solutions, our product and service offerings can help increase precision and productivity for your business.
Consistently Precise Shaped Wire
Turks heads are used for the direct formation of round material to squares, rectangles and special shapes. A turks head machine operates on the rolling mill principle and imparts the same qualities to metal as a rolling mill does: superior surface finish, accurate size and shape, and improved grain structure of the metal. However, turks heads differ from rolling mills in the number and arrangement of rolls. A turks head utilizes two pairs of rolls, one pair is arranged horizontally, while the other is arranged vertically. The material is formed and shaped through the turks head by either a pulling device such as a capstan, or by driven rolls in power-driven models.
Each type of FENN turks head is designed to meet a particular requirement of precision wire or rod shaping. With the exception of power-driven models, all types require a pull-through power source such as a drawbench, bull block, double capstan, a shedding drum or a rolling mill. In both ferrous and nonferrous metal forming industries, turks heads are used as single units and in tandem on common stands for wire and rod shaping.
Turks Heads Benefits
Produce Your Profile
To those unfamiliar with this type of equipment, the question arises – “Why use a turks head in place of other drawing methods?” The Turks Head is a metal forming machine that may be compared to an adjustable draw die, but is largely adjustable within its limiting dimensions.- Turks heads permit forming directly from round to square, rectangles and special shapes
- A turks head can take a bigger reduction per pass, when compared to other forming methods
- Because the rolls are infinitely adjustable there is great flexibility in production capabilities
- Lower maintenance costs since rolls can be reground for continued use
- Turks heads maintain uniform tolerances
- The turks head rolling principle produces less inherent friction
Size Control
The unique design and construction of interlocking slides permit infinite adjustment of the turks head rolls. FENN has engineered the highest possible bearing capacity using precision heavy-duty bearings based on the physical size of each turks head. Built with extreme accuracy by FENN’s highly skilled craftsman, FENN turks heads (when properly used) form sections to close tolerances.Surface Finish
Although surface irregularities cause no particular difficulty, a higher quality entry stock will result in a better finished product. It is important to remove oxides and scale as the build up will cause the rolls to wear more rapidly. It is recommended that lime coatings be removed from wire prior to forming as it tends to build up on rolls and causes separation, tolerance changes, as well as bearing overload.
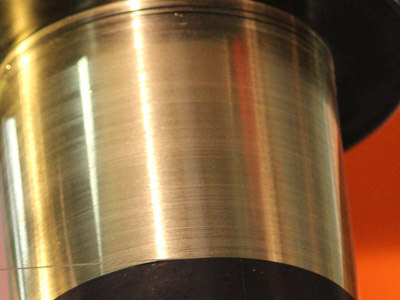
Typical Materials
A variety of metallurgical types can be used with a FENN turks head. Contact us today to learn more about your specific application. A few examples of material types can include Steel, Copper, Platinum, Superconducting, Exotic Metals, and Precious Metals.
Designed Metal Forming Process Solutions
FENN manufactures a range of precision pull-through and power-driven turks heads with high bearing capacities at high speeds. Our design and manufacturing engineers ensure that our metal forming machines hold close uniform tolerances on shaped wire. FENN can design and build customized turks head equipment to act as standalone machinery or be integrated into an existing or new process.
Turks Head Models & Types
Standard & Custom Models to Meet Your Needs
Models are recommended based on the desired wire shape.
Ancillary Options
To obtain high production speeds and hold tolerances within acceptable limits, certain operation rules must be followed. Proper application of the machine equipment is important. The turks head is not intended to be a substitute for a rolling mill, however it can be combined to accomplish certain applications. Particular fundamental rules are applicable to both machines where size control, surface finish, accessories or combination use is applied.
Turks Head Applications
Providing Solutions for these Industries, and MoreSpares & Dies, Made in Connecticut
FENN understands that uptime is key to your business’s productivity and profitability. We offer a full range of spare parts available for both FENN and Torin metal forming machines. With an extensive inventory, FENN can offer a wide array of parts shipped quickly to your door. Our knowledgeable staff will help to ensure you receive the necessary parts to keep your equipment running effectively with minimal downtime. Using FENN spare parts is an essential aspect to maximizing your machine’s efficiency. Don’t know exactly what you need? Our experienced staff will take the time to work with you to understand your unique requirements.
Upgrade Program for Your Aging Machinery
Because FENN machinery upholds a legacy of being quality, reliable and long-lasting, FENN has developed an upgrade program for upgrading, rebuilding or retrofitting your existing FENN equipment. Customers can maximize their machine productivity for aging equipment and extend the machine’s useable life.
We’re Here For You – Training, Support & Service
As a century old company, we are proud of the equipment we design and build, always ensuring it meets your production requirements. We offer comprehensive training programs that can be tailored to meet your business’ needs. Whether you have purchased a new metal forming machine, upgraded existing equipment or your experienced staff is retiring, FENN is available to answer questions and offer training to keep your business productive. Let us know how we can help!